آشنایی با فرآیند تولید ورق استیل و مراحل ذوب و نورد استیل
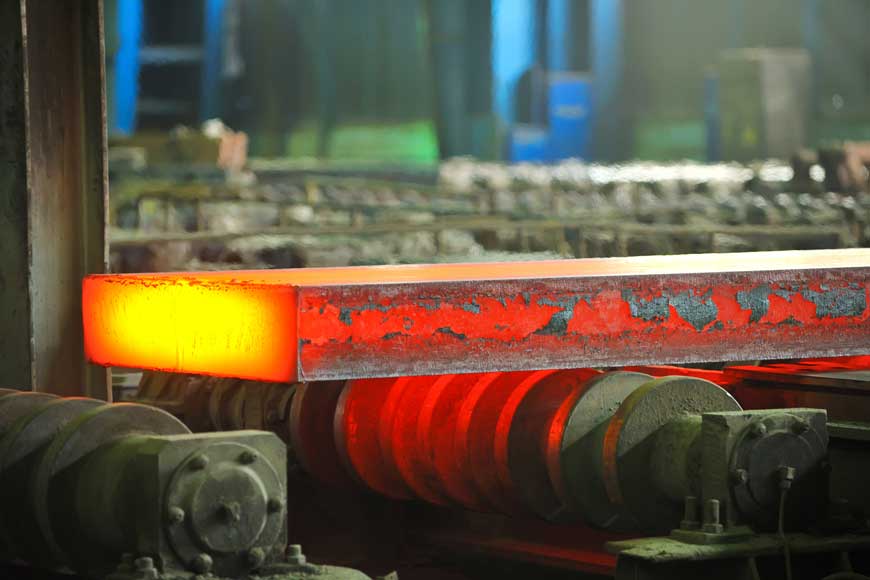
از صنایع فلزی میتوانیم بهعنوان یکی از قدیمیترین صنایع نام ببریم. امروزه کشورهای مختلفی وجود دارند که توانستهاند با تولید فلزات به رشد قابلتوجهی دست پیدا کنند.
امروزه صنایع گوناگون با کارکردهای بسیار متنوع به شکل باورنکردنی وابسطه به انواع فلزات هستند. در این میان ورق استیل یا به عبارتی انواع مقاطع استنلس استیل از جمله مواردی بهحساب میآید که توانستهاند با گسترش چشمگیر در چند دهه اخیر، جای پای خود را در صنایع گوناگون محکم کند. از مواردی که در راستای این موضوع اهمیت بالایی دارد، فرآیند تولید ورق استیل است.
تولید ورق استیل با پشت سر گذاشتن مراحل گوناگونی انجام میشود. در این راستا باید مراحل تولید ورق استیل بادقت تمام انجام شوند. به عبارت دیگر زنجیره تامین فولاد شامل سه مرحله حیاتی است، که عبارتند از کارخانه ذوب و آلیاژسازی، کارخانه نورد مجدد و مراکز وکارخانجات خدمات تکمیلی.
البته مراحل دیگری در زنجیره تامین و سطوح مختلف فراتر از این سه وجود دارد. با توجه به اینکه ذوب و آلیاژ سازی، نورد مجدد دقیق، و خدمات تکمیلی، نقشهای ویژه و حیاتی در تولید فولاد ضد زنگ و فلزات خاص هستند.
فرآیند تولید ورق استیل به چه صورت است؟
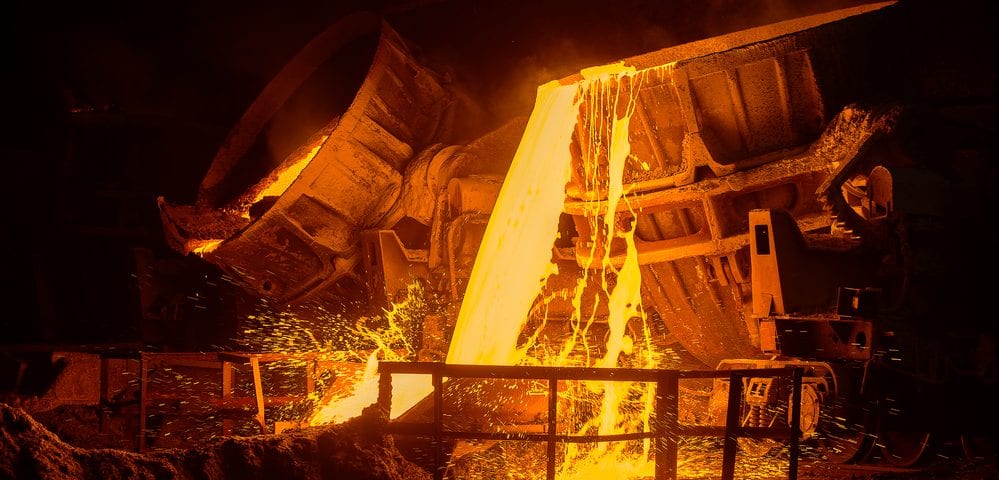
تمام اقلام و مواد اولیه فلزی از جمله ورق استیل زنجیره تامینشان از کارخانه ذوب آغاز میشود. از کارخانه ذوب، محصول تولیدی به شکل شمش، بیلت و اسلب معمولاً به مراکز نورد و خدمات تکمیلی ارسال میشود.
البته این موضوع به نوع آلیاژ، ضخامت و کاربرد آن نهایی آن بستگی دارد. این فلز ممکن است قبل از اینکه به مصرف کننده نهایی برسد، از مراحل بیشتری از زنجیره تامین مانند ریختهگران، فورجکاران، قطعه سازان یا پرسکاران گذر کند.
اکثر صنعتگران بخش، نورد مجدد و مراکز خدمات تکمیلی را بهعنوان نقاطی یکسان در نظر میگیرند، اما ممکن است همیشه اینطور نباشد.
مرحله اول ذوب فلزات
کارخانه ذوب که به عنوان کارخانه فولاد سازی نیز شناخته می شود، نقش مهمی در زنجیره تامین فولاد ضدزنگ دارد. این جایی است که مواد فلزی جدید و بازیافتی با هم ذوب میشوند تا اسلب فولادی ضدزنگ یا اشکال دیگر مانند بیلت، شمش را تشکیل دهند.
کارخانه ذوب ترکیبی از مواد اولیه فولاد ضدزنگ بازیافتی و بکر را جمع آوری و فراوری میکنند تا گریدهای مختلف استیل را بدست آورند. معمولاً ترکیب ورودی این کورههای ذوب حدود 90% فولاد بازیافتی و 10% فولاد بکر است. این ترکیب هم در مورد فولاد ضدزنگ یا استیل و هم در مورد فولاد کربنی صدق میکند.
مواد بازیافتی میتوانند از منابع مختلفی مانند اقلام مصرفی معمولی فولاد ضدزنگ که بازیافت میشوند و ضایعات از فروشندگان و مصرفکنندگان تامین شوند.
تامین کنندگان ضایعات با مراکز نورد دقیق، مراکز خدمات تکمیلی و قطعهسازان برای خرید و دستهبندی «ضایعات دقیق» که قبلاً بر اساس آلیاژهای مختلف طبقهبندی شدهاند و از ناخالصیهای درون فلز جلوگیری میکنند، ارتباط دارند.
سپس تامین کنندگان ضایعات این مواد را دوباره به کارخانه ذوب می فروشند و در آنجا مجدداً بررسی و مرتب میشوند تا به همراه مواد اولیه دیگر ذوب شوند و محصولات فلزی که ما میشناسیم مانند اسلب، بیلت و شمش تولید شوند.
پس برای اینکه بتوانید ورق استیل را تولید کنید، در ابتدا نیاز است ضایعات مناسب تامین و ذوب شوند. این ضایعات دارای ترکیبات شیمیایی مختلفی هستند و در کارخانه ذوب پیشرفته میتوانید به هر یک از این ترکیبات را کنترل و تنظیم کنید. برای ذوب کردن فولاد به یک کوره قوس الکتریکی نیاز است.
این کوره باید دارای ظرفیت حداقل 160 تن باشد. بعد از اینکه فلز مذاب آماده شد، باید آن را به یک مبدل منتقل کرد. همچنین برای اینکه بتوان به ترکیبات شیمیایی مورد نظر رسید، نیاز است یک سری از عناصر آلیاژی به آن اضافه شوند.
با درنظرگرفتن تمامی این موارد تولید گریدهای استاندارد کار سختی نخواهد بود ولی نیاز به فناوری خاص خود را دارد. آلیاژ مذاب باید سرد و منجمد شود که این فرایند طی مراحل ریختهگری با روشهای خاص به انجام میرسد.
اکثر کارخانههاس امروزی از کورههای قوس الکتریکی سازگار با محیط زیست استفاده میکنند؛ بر خلاف کورههای بلند سنتی که در گذشته مرسوم بودند.
این فناوری جایگزین انرژی کمتری مصرف میکند و انتشار کربن در محیط زیست به میزان قابل توجهی کاهش یافته. همچنین، شرکتهای صنعت فولاد ضدزنگ مشتاق هستند تا ضایعات را تا حد امکان به حداقل برسانند.
آنها هر قطعه محصولی را که معمولاً در طول تولید دور ریخته میشود جمع آوری و جدا میکنند. تمام این قراضهها بعداً در کوره الکتریکی ذوب میشود و به چرخه تولید باز میگردد.
کورههای مختلف مورد استفاده در کارخانه ذوب وظیفه ذوب فولاد را بر عهده دارند. ترکیب شیمیایی فلز نیز با کاهش عناصر آلیاژی و افزودن عناصر دیگر برای دستیابی به خلوص مطلوب تنظیم میشود.
خط ریختهگری پیوسته اسلب در یک کارخانه ذوب، فولاد مذاب را به یک نوار فولادی پیوسته با ضخامت حدود 60 میلیمتر تبدیل میکنند.
این محصول را میتوان با چند مرحله نورد گرم، مقرون به صرفه و سریع به ورق یا انواع محصولات تخت فولادی تبدیل کرد. فلز همچنین میتواند با طی مراحل دیگر تولیدی به مفتول، لوله، پروفیل، مقاطع توپُر و اشکال مختلف دیگر تبدیل شود.
اسلبها با آب خنک شده تا کاملاً جامد شوند و در یک کارخانه نورد گرم به محصولات مورد نظر تبدیل شوند. سپس ورق نورد گرم حاصل به کویل تبدیل میشود و سپس در کارخانه نورد سرد به اندازههای دقیق رسیده و نهایتاً به صورت شیمیایی پاکسازی میشوند تا ورق استیل آماده مصرف در صنایع مختلف شود.
لازم به توضیح است که محصول کارخانه ذوب و نورد گرم میتوانند به صورت ورق تخت باشد، اما معمولاً در این مرحله کیفیت سطحی خشنتر و از نظر ابعادی تلرانسها بازتر هستند.
این امر باعث میشود که این محصول برای طیف وسیعی از کاربردهای تخصصی در صنایعی مانند پزشکی، غذایی، ساختمانی و هوافضا غیر قابل استفاده باشد.
اینجاست که نقش مهم فرایند نورد مجدد فولاد ضدزنگ که انواع فولاد با ویژگیهای متمایز را برای صنایع یا کاربردهای خاص فرآوری میکند، مورد توجه قرار میگیرد.
مرحله بعدی نورد مجدد ورق استیل است
نورد مجدد فولاد ضدزنگ نقش مهمی در زنجیره تولید ورق استیل دارد. همانطور که از نام آن پیداست، این فرآیند شامل نورد مجدد فلز برای تولید مواد در گیجها یا ضخامتهای کمتر با تحمل بارهای بیشتر و دقت و کیفیت بالاتر میشود. این فرآیند معمولاً برای ورق استیل مورد استفاده برای تولید کاربردهای پزشکی، غذایی، دکوراتیو، هوافضا و صنایع پیشرفته ضروری است.
مشابه کارخانه ذوب، کورههایی نیز در کارخانهجات نورد مجدد وجود دارد. مواد اولیه پس از مرحله پیشگرم به شکل نواری وارد دستگاههای نورد شده و با کاهش ضخامت به ورقهای استیل نازکتر تبدیل میشوند.
با این حال، به دلیل خواص مکانیکی فولاد ضدزنگ، برای اکثر ضخامتها نمیتوان این کار را در یک مرحله انجام داد. قبل از اینکه برای ضخامتهای بسیار نازک نورد شود، باید در بین مراحل نورد به طور متوسط آنیل شود (گرم شود) تا استرس ناشی از نورد کاهش یابد.
بقیه فرآیند نورد معمولاً در دمای اتاق و بصورت نورد سرد اتفاق میافتد. در تمام این فرآیندها، تجهیزات و سیستمهای پیشرفته برای کنترل و اندازهگیری ضخامت دقیق مواد در کل کویل ورق استفاده میشود.
فرآیند نورد سرد عیوب فلزی مانند چروکخوردگی را رفع و ساختار فلز را فشرده و خواص مکانیکی و فیزیکی را بهبود میدهد. ویژگیهایی که یک نورد مجدد دقیق میتواند به یک ماده اضافه کند، آن را برای مشتریانی که ثبات و دقت در خواص یا تولرانسهای محصول نهایی برایشان مهم است و ارزش دارد انتخابی ضروری است.
زمانی که ورق استیل برای کاربردی دارای الزامات خاصی است که با خدمات تکمیلی نمیتوان آنها را برآورده کرد، مصرفکنندگان باید خرید از یک کارخانه نورد سرد دقیق را در نظر داشته باشند.
کارخانههای نورد شرکای حیاتی برای تولیدکنندگانی هستند که در توسعه محصول فعالیت میکنند. یک کارخانه نورد متخصص، تیم مهندسین و متالورژیستهای خود را برای کمک به مشتریان جهت پیادهسازی نیازها در محصول استیل خود و سایر چالشهای تولیدی که منحصراً برای فرآیندهای تولید و کاربرد مشتری مناسب است، مستقر میکند.
توضیح بیشتر در مورد مرحله نورد گرم
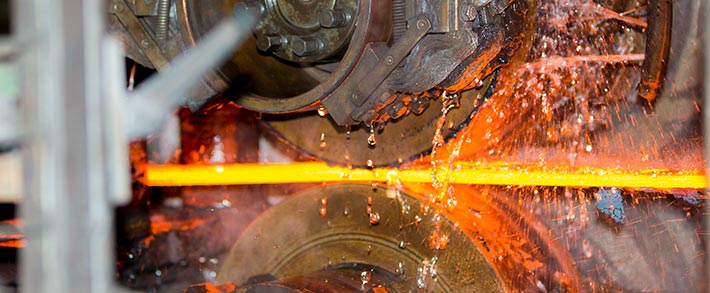
فرآیند تولید ورق استیل نورد گرم بسیار پراهمیت است. در نورد گرم ورق استیل کاهش ضخامت ورق در چندین مرحله نورد صورت میگیرد. همانطور که گفتیم برای این کار نیاز است ورقها مجدد گرم شوند. برای گرمکردن دوباره ورق باید آن را داخل کورهای با دمای 1250 درجه سانتیگراد قرار دهند.
برای اینکه ورقها بتوانند به ضخامت دلخواه و مورد نیاز برسند، بطور متوسط باید 7 مرحله نورد طی شود. ازآنجاییکه ورق استیل دارای سطح اکسیدی است، بعد از سردشدن ورق با سطحی خشن و پوسته پوسته با رنگ مات بدست میآید.
به همین دلیل لازم است کویل ورق استیل بهدستآمده را به کمک عملیات مکانیکی، شیمیایی و حرارتی به کیفیت مطلوب برسانیم.
عملیات حرارتی آنیل و اسیدشویی برای بهبود کیفیت ورق استیل
در این مرحله از فرآیند تولید ورق استیل باید خواص سطحی و مکانیکی ورق استیل تا حد بسیار زیادی بهبود پیدا کنند. ازآنجاییکه این کویلها کیفیت ظاهری مطلوبی ندارند، در صنایعی استفاده میشوند که زیبایی در آنها ملاک نباشد.
البته کویلهای نورد گرم استیل را باید در کورههای مخصوص قرار دهیم تا بهخوبی حرارت ببینند. این کورهها مخصوص عملیات حرارتی آنیل کردن هستند.
با این کار میتوان نسبت به بهبود خواص مکانیکی ورق استیل اقدام کرد و ساختار متالورژیکی ورق بدست آمده را یکنواخت کرد.
حالا نوبت آن است تا سطح کویلها را از اکسیدهای فلزی نامطلوب پالایش کنیم. برای این کار گاهی از عملیات شات بلاست بهره برده میشود.
برای شستشوی شیمیایی یا اسید شویی نیاز است از حمامهای اسید استفاده شود. همچنین فرایند خشککردن نیز در هوای آزاد به انجام میرسد. نتیجهای که میتوانید در انتهای این مراحل مشاهده کنید، سفیدشدن وجلای سطح ورق استیل در حد No.1 یا 1D است؛ بدون اینکه کوچکترین اکسیدی به چشم بخورد.
در این مرحله کویلهایی که به رنگ سفید تغییر پیدا کردهاند میتوانند وارد بازار شوند و نیازی نیست روی آنها پرداخت سطح یا نورد سرد صورت بگیرد.
مرحله نورد سرد و عملیات حرارتی نهایی آنیل کردن
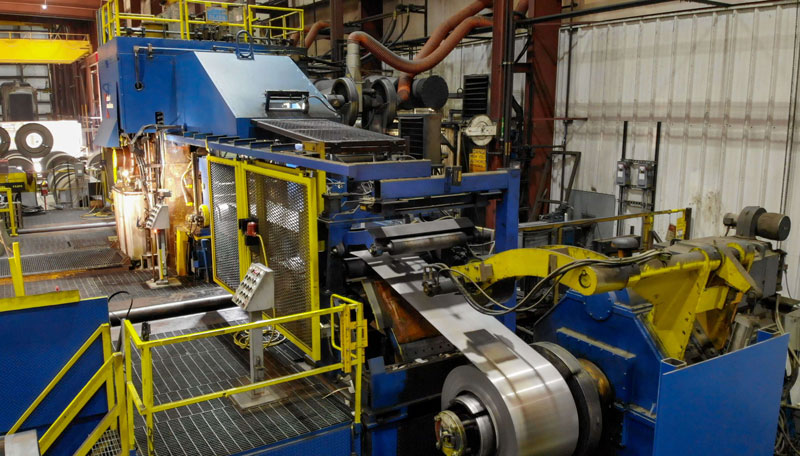
در این بخش از فرآیند تولید ورق استیل نیازها و خواستههای مشتری موردتوجه قرار میگیرند. یعنی باتوجه به مشخصات مورد نظر مشتری، ضخامت ورق استیل را کاهش داده و سایر مشخصات سطحی و ابعادی را روی ورق اعمال میکنند. برای بهبود خواص مکانیکی نیز عملیات حرارتی نهایی آنیل وارد عمل میشود.
زمانی که فرایند نورد سرد به انجام میرسد، سطح ورقها کاملاً پرداخت میشود و برای کاربردهای زیادی آماده میگردد. تولید لوازم منزل و کاربردهای دکوراتیو نمونههایی از این کاربردها است.
در فرایند نورد سرد مجدداً شاهد کاهش ضخامت کویلهای ورق استیل خواهیم بود. البته لازم به ذکر است در کنار کاهش ضخامت، کیفیت نیز تا حد بسیار زیادی افزایش پیدا میکند.
بعد از اینکه نورد سرد انجام شد، عملیات نهایی شامل پرداختکاریهای خاص و برخی عملیات حرارتی درصورت نیاز انجام میشود. این مراحل برای بهبود خواص سطحی و مکانیکی ورق استنلس استیل است.
بهطورکلی آنیلکردن میتواند باعث بهبود چقرمگی و شکلپذیری ورق شود که یک امتیاز مثبت بهحساب میآید.
برای اینکه ورق به بالاترین سطح از پرداخت و جلای فلزی دست پیدا کند، باید فرایند حرارتی آنیل در محیطی صورت بگیرد که از اتمسفر آن محافظت شده است. خوشبختانه هیچگونه اکسیدی در این مرحله ایجاد نخواهد شد؛ ازاینرو نیازی به شستشو نیست.
میتوانید از سطح ورق تولیدشده پرداخت درخشان را به چشم ببینید. برای اینکه بتوان صافی ورق را تضمین کرد، پیشنهاد میشود عملیات و پاسهای نورد سطحی به میزان کافی به انجام برسد.
برای اینکه بتوان این مرحله را پشت سر گذاشت، به یک تا سه پاس نورد سرد نیاز خواهد بود که ما را به سطوحی همچون BA و 2B خواهد رساند. این سطوح مناسبترین گزینهها برای تولید لوازم خانه هستند.
مرحله نهایی خدمات و عملیات تکمیلی ورق استیل است
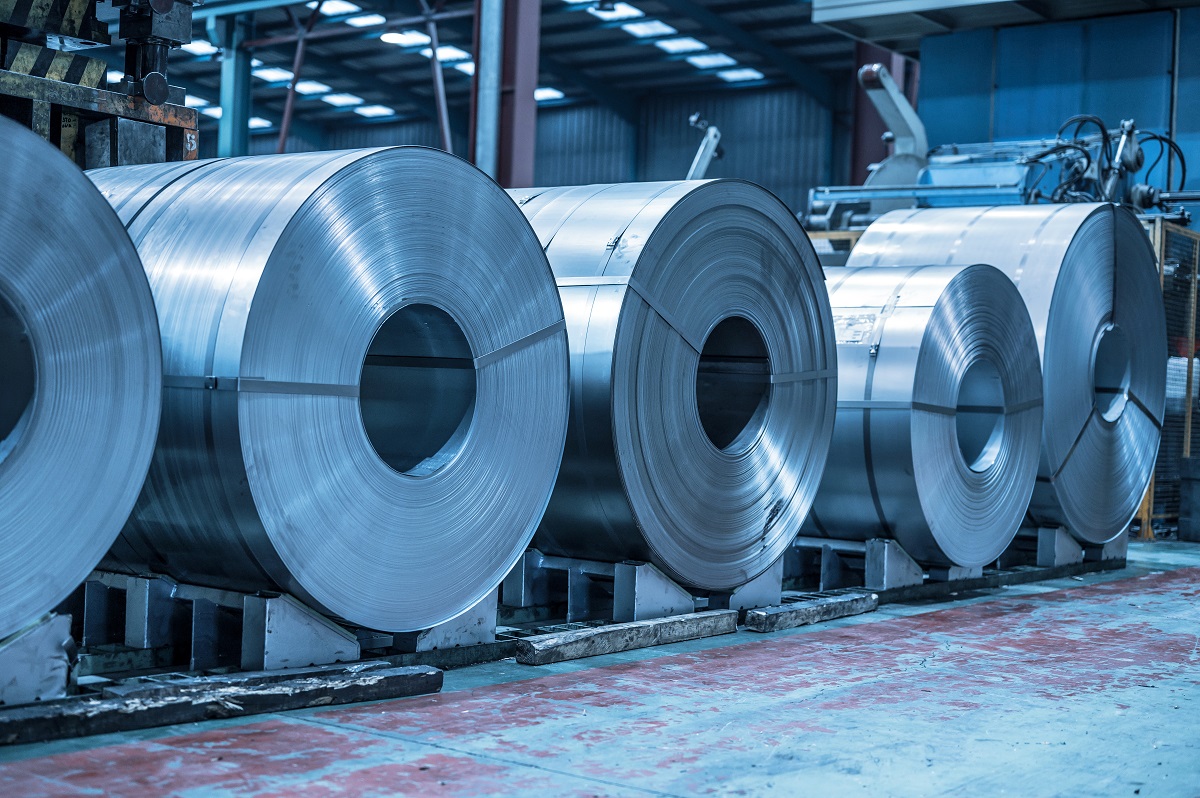
یکی دیگر از نقشهای حیاتی در زنجیره تامین فولاد، خدمات و عملیات تکمیلی فولاد ضدزنگ است. یک مرکز خدمات تکمیلی با انواع مختلفی از فولاد از کارخانه ذوب یا کارخانههای نورد مجدد سروکار دارد. این مراکز دارای انبارهای بزرگ ذخیره سازی مواد اولیه برای تضمین تامین منظم خطوط تولید خود هستند.
پس از دریافت مواد اولیه، خدمات فنی تکمیلی قبل از فروش مجدد به مشتریان انجام میشود. برخی از فعالیتهای انجام شده در اینجا ممکن است شامل خمکاری و اضافه کردن لبههای مختلف یا برش مواد به عرضهای مختلف باشد.
فعالیتهایی که میتواند در یک مرکز خدمات فنی انجام شود، به غیر از انبارش مواد، شامل مسطح سازی ورق کویل و برش عرضی و کنار ورق بر اساس سفارش مشتری است.
به عنوان خدمات فنی در این مرحله طبق نظر مشتری عملیات تکمیلی بسیار متنوعی قابل انجام است.
از جمله این عملیات میتوانیم به پولیشکاری، برسکاری، آبکاری PVD و… اشاره داشته باشیم.
ورقهای استیل تولیدشده این قابلیت را دارند که با انواع عملیات فرمدهی و برش به شکلهای مختلف در بیایند و در صنایع گوناگون مورد استفاده قرار بگیرند.
.