ریخته گری ماسه ای
ریخته گری ماسه ای
ریخته گری ماسه ای یکی از روش های ریخته گری برای تولید قطعات فلزی است که از گذشته تا به امروز انجام می شود و با پیشرفت علم، این صنعت نیز پیشرفت کرده است. ریخته گری ماسه ای اغلب برای قالب سازی قطعات استفاده می شود؛ زیرا ماسه ها در برابر آتش و گرما مقاوم بوده و به اصطلاح نسوز هستند.
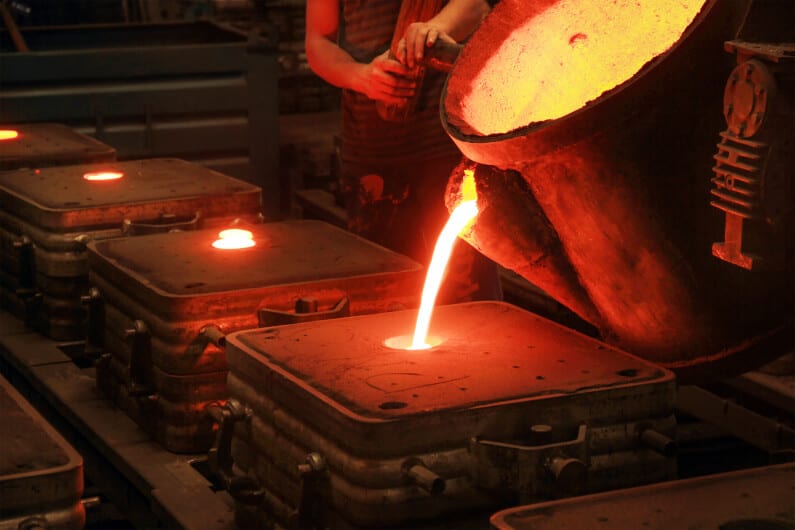
ریخته گری ماسهای چیست؟
ریخته گری ماسهای به طور معمول به مواد مبتنی بر سیلیس، مانند ماسههای مصنوعی یا طبیعی متکی است. ماسه ریخته گری به طور کلی از شن و دانههای کروی ریز تشکیل شده است که میتوان آنها را محکم در یک سطح قالب صاف جمع کرد.
فرایند ریخته گری به گونهای طراحی شده است که با اجازه دادن درجه متوسطی انعطاف پذیری و انقباض در مرحله خنک کننده، پتانسیل پارگی، ترک خوردگی و سایر عیوب را کاهش میدهد.
همچنین، در فرایند ریختهگری ماسهای، خاک رس به عنوان ماده اتصال عمل میکند و شن و ماسه با افزودن خاک رس تقویت میشوند و به هم چسبیده میشوند.
قطعات اتومبیل مانند بلوکهای موتور از طریق فرایند ریخته گری ماسهای تولید میشوند.
ریخته گری ماسه، شامل مراحل مختلفی از جمله ساختن الگو، قالب سازی، ذوب و ریختن مذاب و تمیز کردن است. در واقع، الگو، شکلی است که در اطراف آن ماسهها فشرده شدهاند.
پس از فشرده شدن شن و ماسه به اندازه کافی برای تکثیر نمونه و الگو، قالب برداشته میشود و الگو و نمونه استخراج میشود.
پس از ریختن مذاب و منجمد شدن آن، عملیات ریخته گری به اتمام میرسد. نمونه از قالب برداشته شده و از هرگونه شن و ماسه چسبنده تمیز میشود.
فرایند انجام کار ریخته گری ماسه ای
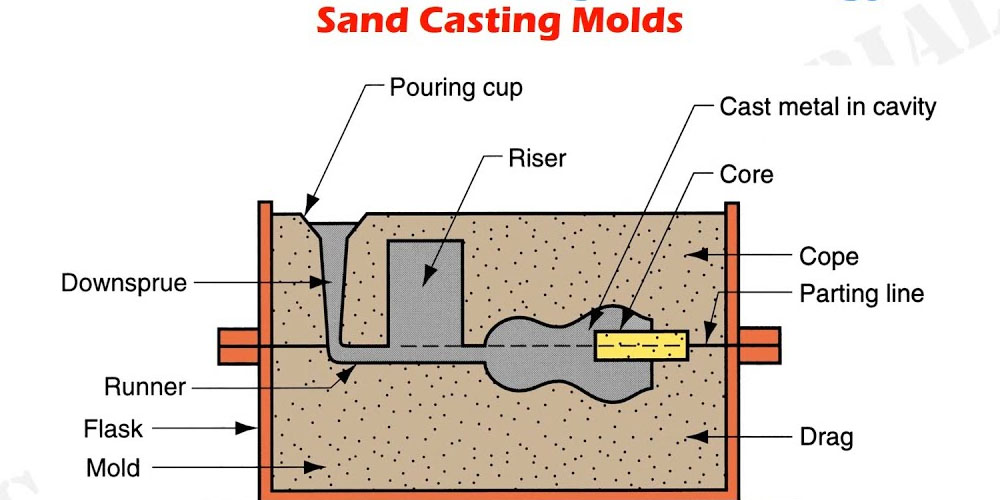
ریخته گری ماسه ای یک فرایند ریخته گری است که در آن از ماسه برای ایجاد قالب استفاده می شود و پس از آن فلز مایع برای ایجاد قطعه در این قالب ریخته می شود .
ماسه ای که در این روش استفاده می شود عایق بندی خوبی دارد و نسبتاً ارزان است. مراحل مشخصی برای این فرآیند وجود دارد و این مقاله هر یک از این مراحل را طی می کند تا دقیقاً نحوه انجام این روش ریخته گری را نشان دهد .
1-مرحله اول
در فرایند ریخته گری ماسه ای ساخت الگوی ریخته گری برای قالب است. این الگوها غالباً از موادی مانند چوب یا پلاستیک ساخته می شوند و بیش از اندازه بزرگ هستند تا در هنگام خنک شدن، فلز ریخته شده کوچک شود.
آن ها برای ایجاد قالب ماسه برای قسمت نهایی استفاده می شوند، و بسته به مواد الگو می توانند دوباره مورد استفاده قرار گیرند. اغلب اوقات، دو نیمه الگوی به طور جداگانه ایجاد می شود که حفره ها راکنار هم قرار می دهد.
هسته ها درز های قالب داخلی هستند که در صورت نیاز به خطوط داخلی نیز می توانند مورد استفاده قرار گیرند ، اما به طور معمول بعد از یک ریخته گری یکبار مصرف می شوند.
نوع الگو و مواد آن نه تنها توسط ابعاد قطعه مورد نظر بلکه به تعداد ریخته گری مورد نیاز از هر اندازه قالب است.
2-مرحله دوم
فرایند ساخت قالب های ماسه از این الگوها است. قالب ماسه معمولاً در دو نیمه انجام می شود، جایی که یک طرف قالب با یک الگو و یک طرف دیگر با استفاده از الگوی دیگر ساخته می شود. گرچه ممکن است قالب ها همیشه در دو نصف نباشند، این ترتیب آسان ترین روش را برای ایجاد قالب و دستیابی به قطعه، پس از ریخته شدن فراهم می کند.
اپراتور باید به طور محکم ماسه را در هر الگو بسته بندی کند تا اطمینان حاصل شود که ماسه شل وجود ندارد و این کار را می توان با دست یا ماشین انجام داد.
پس از کوبیدن، الگوها برداشته می شوند و خطوط بیرونی خود را درماسه باقی می گذارند، جایی که تولید کنندگان می توانند کانال ها و اتصالات ( معروف به راهگاه یا گلویی ) را به داخل کشش و یک قیف در رو به رو ایجاد کنند (معروف به “مذاب رو”).
این راهگاه / گلویی و مذاب رو برای ریخته گری دقیق لازم هستند، زیرا گلویی و راهگاه ها اجازه می دهند فلز به هر قسمت از قالب وارد شود در حالی که مذاب رو امکان ریختن راحت درون قالب را فراهم می کند.
3-مرحله سوم
این مرحله اصلی در ریخته گری ماسه ای ساخت یک قالب کامل است. اگر برای برخی از خطوط داخلی به یک هسته نیاز باشد، قبل از مرحله بستن در قالب قرار می گیرد و همچنین هر نوع راهگاه / گلویی نیز از نظر عدم انطباق بررسی می شود.
4-مرحله چهارم
زمانی شروع می شود که ماده نهایی مورد نظر ( فلز ) در کوره ذوب شود و سپس در قالب ریخته شود. آن را با احتیاط داخل شیار قالب با ملاقه ریخته، در آن جا فلز مذاب با حفره ای که الگوها از آن خارج می شود مطابقت می یابد و سپس می گذارد تا کاملاً خنک شود.
پس ازسرد شدن فلز، ماسه را از قالب خارج می کنند تا قطعه نهایی را آشکار کنند.
5-مرحله پنجم ( نهایی )
مرحله تصفیه کردن است، جایی که قطعه نهایی خود تصفیه می شود. این تصفیه شامل برداشتن سیستم راهگاه و گلویی و همچنین باقی مانده قطعات قالب باقی مانده در قطعه نهایی است.
قطعه در سطح ریخته گری می تواند سمباده کاری وصیقل داده شود.
پس ازتصفیه کردن اساسی، هر قسمت از نظر نقص بررسی می شود و برای اطمینان از انطباق با استانداردهای کیفیت سازنده آزمایش می شود تا عملکرد مطابق برنامه های مربوطه را داشته باشد.
مزایای ریخته گری ماسهای
ریختهگری ماسهای مزایای زیادی دارد که مزایای اصلی این فرایند ریخته گری در ادامه آورده شده است:
1-هزینههای تولید نسبتاً ارزان، به خصوص در نمونههای کم حجم.
2-توانایی ساخت قطعات بزرگ.
3-ظرفیت ریخته گری مواد آهنی و همچنین مواد غیر آهنی.
4-هزینه کم ابزار برای فرآیندهای پس از ریخته گری.
معایب ریخته گری ماسهای
علارغم فواید آن، ریخته گری ماسهای معایبی نیز داردکه در ادامه به آنها اشاره شده است:
1-دقت ابعادی پایینتر ریختهگری ماسهای نسبت به سایر فرایندهای ریخته گری
2-وزن ریختهشده معمولاً از وزن محاسبه شده بیشتر است.
3-سطح نهایی قطعه ریختهگری شده آهنی معمولاً از RMS125 فراتر میرود.
4-علاوه بر این، این فرایند تمایل به تولید محصولاتی با سطح نسبتاً خشن دارد.
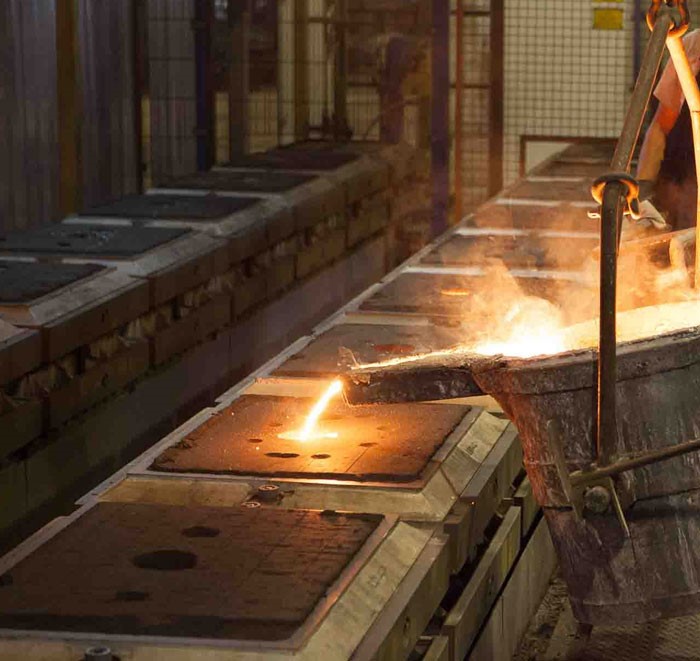
.